IAS案例研究:自动化测试实验室
IAS营销总监Kyle Weise解释说:“客户一直在使用100多名员工,每个人分别完成产品测试周期的整个准备工作。” “这包括繁琐的操作,例如准备托盘,单独放置种子以及手动记录托盘和种子数据。”
最初是一个使单个任务自动化的项目,后来又变得更大了–寻找一种使整个种子测试实验室自动化的方法。目标很快变得更加复杂和多方面。
Kyle说:“客户使用的是临时工,培训很少。” “存在质量控制,高离职率和高人工成本的问题。”
数据完整性也存在问题。客户需要对每个种子批次中要获取和跟踪的数据有更大的信心。
由于测试过程的程序是高度重复的,并且需要严格的控制参数,因此它们是利用机器人自动化的精度和效率的理想选择。
设计解决方案
IAS通过访问客户的种子测试实验室来开始该项目,与现场的工人和关键人员进行交谈。
Kyle说:“我们相信优秀的系统可以适应公司的内部流程。” “因此,当我们进行类似这样的复杂项目时,我们喜欢从发言开始并与关键人物会面。 我们了解他们的工作方式以及他们认为可以改进的地方,并使用这些信息来构建更好的系统。”
IAS很快了解到,实验室中的每个操作区域都是相互依赖的,因此对于他们而言,关键是要首先将每个区域分成模块并布局中央架构。 一旦工程师完成了这些工作,他们就可以在维护中央控制框架的同时更有效地划分工作。
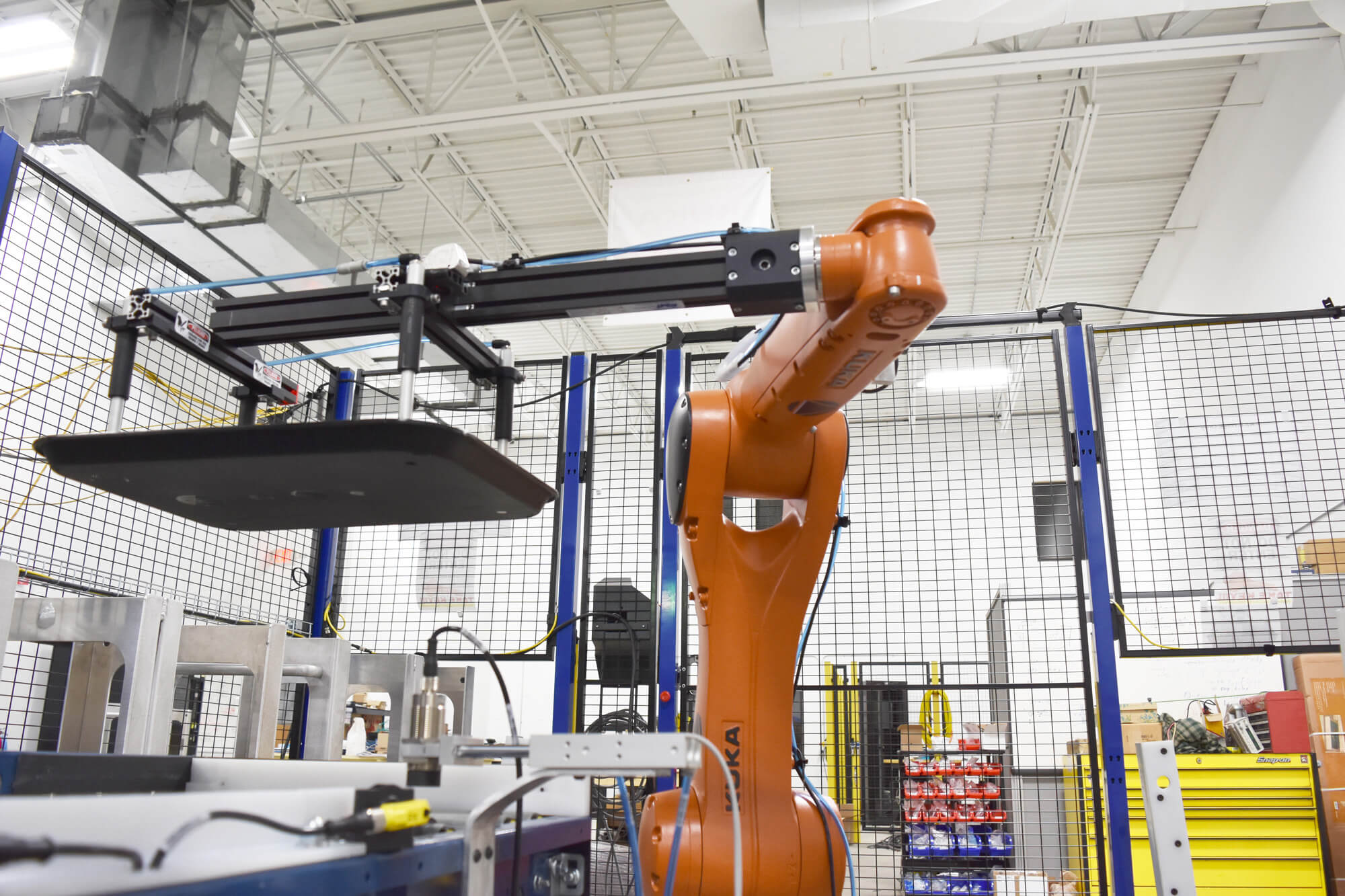
为了帮助验证该概念并将其解释给客户,IAS使用了Visual Components 3D制造模拟软件。
Kyle说:“使用MIoT.VC创建布局并模拟我们的设计,我们就能向客户充分展示我们团队的创造力和能力。”
MIoT.VC还帮助保持了项目早期的动力并改善了沟通。
“能够向客户展示系统操作的仿真和虚拟模型,获得反馈并快速调整设计的能力; 确实有助于简化反馈循环。” Kyle说。
“客户为即将到来的事情感到准备,所有利益相关者对需要做的事情都有清楚的了解。”
流程
为该项目提供的解决方案IAS包括六个关键站点:卸载托盘,从容器中解开种子,应用种子,检查种子网格,将种子夯实到位以及装载控制车。 该过程从纸盘卸货站开始。
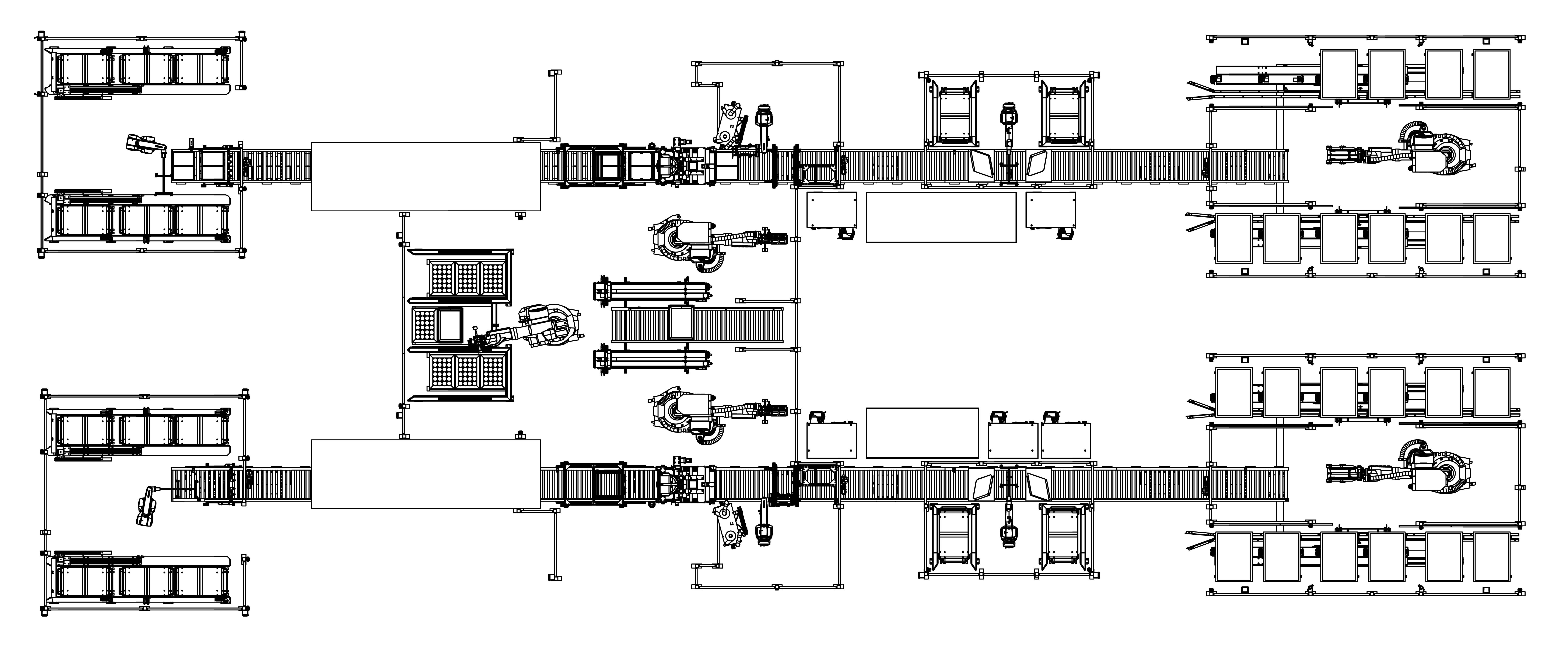
“在托盘卸货站,机器人会从推车上卸下空托盘。”Kyle解析说, “然后将托盘准备播种,方法是将营养胶涂在托盘上或在托盘顶部放一块湿纸。然后将托盘沿着生产线发送到播种站。”
同时,将装满种子的广口瓶送入机器人的非震击站,在那里,机器人将广口瓶从推车上移开,旋开盖子,然后将其放在双皮带输送机上。传送带将罐子带到另一个机器人,该机器人将种子提起并倒入分配系统。然后将空罐子放回输送机系统上并送走。
在播种站,分配系统以10 x 10的模式将种子均匀地滚动到托盘上。然后将托盘移至检查站,在检查站成像,以确认播种方式正确,并检测到任何非种子或有缺陷的种子。然后,采摘机械手用同一批中的其他种子替换非种子和有缺陷的种子,并调整托盘上的种子以确保它们适合模式。
设计检查过程是该项目更具技术挑战性的方面之一。
Kyle说:“对有机物进行详细检查可能很困难,因为定义缺陷参数通常是一项挑战。” “诸如颜色,形状和大小之类的因素都可以是可变的,但不能完整地表明通过/失败标准。”
“我们使用机器学习来解决这些问题。我们的视觉团队围绕种子集的参数训练了一个神经网络,将其部署到系统中后,我们看到了很好的结果。”
在检查过程之后,将托盘发送到自动夯实站,在此处将种子夯实在托盘上。然后,将托盘发送到机械手装卸站,然后将其装载到推车上并进行索引。装满后,推车被送入控制室,使种子发芽。
测试后,将空托盘从控制室中运出,并自动卸载,成像,清洗并重新装载到能够在生产线开始时重新进入系统的相同的车中。
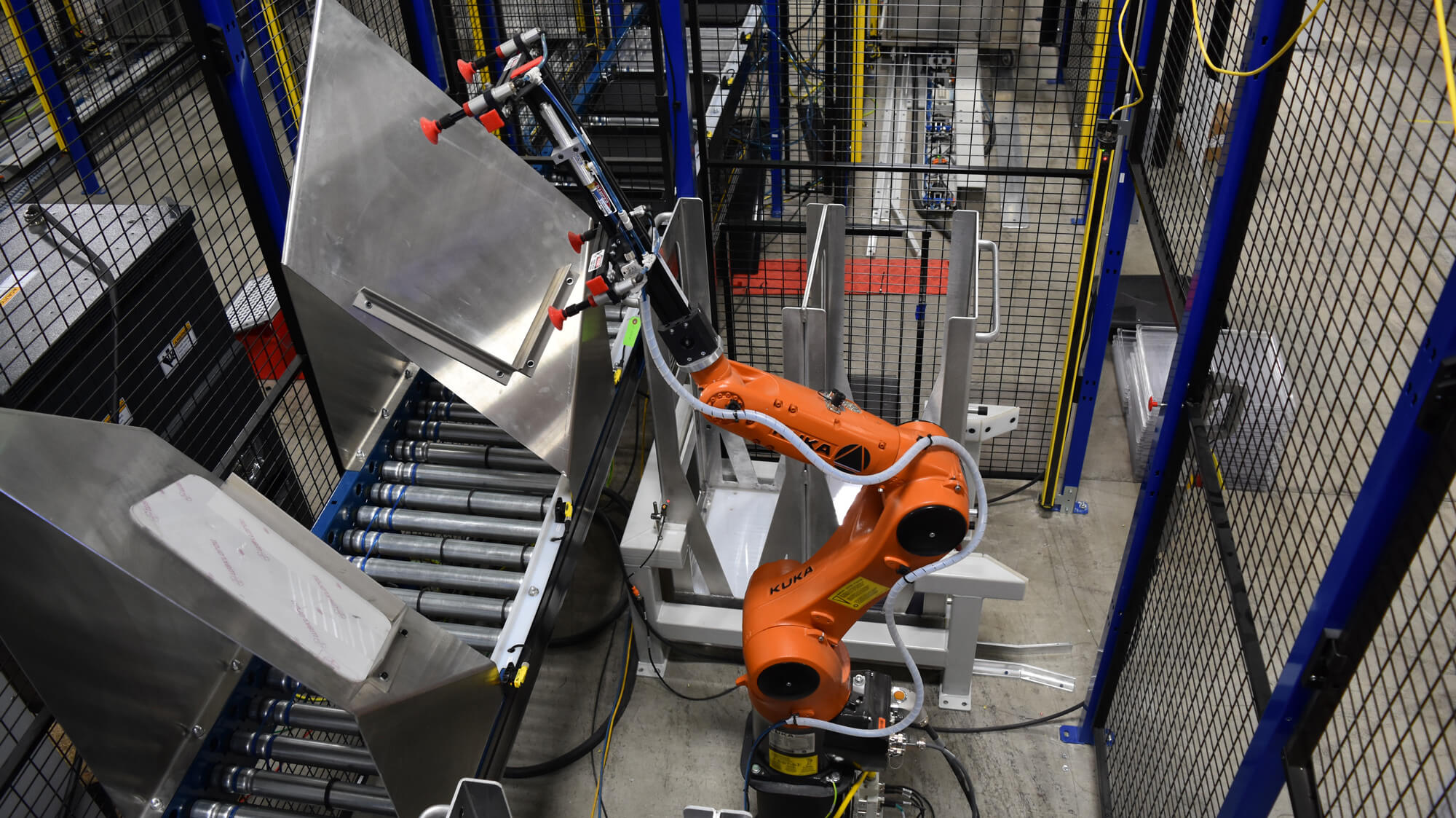
结果
完整的在线系统包括12个机器人,13个摄像头和各种RFID读/写区域。 在控制室入口处还使用了另外15个集成摄像头来监控推车活动。 IAS为此客户的种子测试过程设计了量身定制的自动化解决方案。
Kyle说:“ IAS能够提供完整的工程解决方案。” “这包括机电系统的设计,编程,测试,构建和安装。”
该项目的结果是提高了产量并减少了人工成本。 此外,IAS成功地使客户对其数据充满信心。
“客户现在可以完全跟踪整个过程,” Kyle说。 “从数据分析的角度来看,它们具有更高的数据保证和可追溯性。”